Electromechanical
Electromechanical components convert electrical energy into mechanical motion, convert mechanical motion into electrical energy, or facilitate electrical interconnection.
Components we were using in previous topic and will use in the following topics:
- Servomotor;
Servomotor
A servomotor is a rotary actuator or linear actuator that allows for precise control of angular or linear position, velocity and acceleration. It consists of a suitable motor coupled to a sensor for position feedback. It also requires a relatively sophisticated controller, often a dedicated module designed specifically for use with servomotors.
Servomotors are not a specific class of motor, although the term servomotor is often used to refer to a motor suitable for use in a closed-loop control system.
Servomotors are used in applications such as robotics, CNC machinery or automated manufacturing.
MechanismA servomotor is a closed-loop servomechanism that uses position feedback to control its motion and final position. The input to its control is a signal (either analogue or digital) representing the position commanded for the output shaft.
The motor is paired with some type of position encoder to provide position and speed feedback. In the simplest case, only the position is measured. The measured position of the output is compared to the command position, the external input to the controller. If the output position differs from that required, an error signal is generated which then causes the motor to rotate in either direction, as needed to bring the output shaft to the appropriate position. As the positions approach, the error signal reduces to zero and the motor stops.
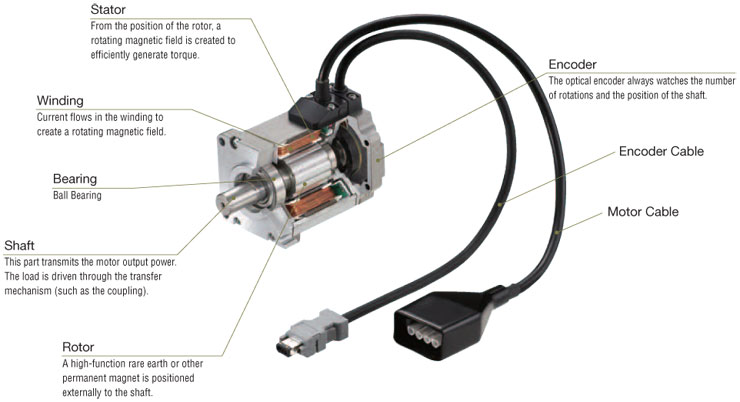
Encoders
Simple servomotors may use resistive potentiometers as their position encoder. These are only used at the very simplest and cheapest level, and are in close competition with stepper motors. They suffer from wear and electrical noise in the potentiometer track. Although it would be possible to electrically differentiate their position signal to obtain a speed signal, PID controllers that can make use of such a speed signal generally warrant a more precise encoder.
Modern servomotors use rotary encoders, either absolute or incremental. Absolute encoders can determine their position at power-on, but are more complicated and expensive. Incremental encoders are simpler, cheaper and work at faster speeds. Incremental systems, like stepper motors, often combine their inherent ability to measure intervals of rotation with a simple zero-position sensor to set their position at start-up.
Instead of servomotors, sometimes a motor with a separate, external linear encoder is used.These motor + linear encoder systems avoid inaccuracies in the drivetrain between the motor and linear carriage, but their design is made more complicated as they are no longer a pre-packaged factory-made system.